My first post in this series (see here) looked at the reasons Highlands and Islands Enterprise (HIE) gave to the Public Accounts Committee about why they decided to build the funicular out of concrete rather than steel. These came down to cost but no evidence was provided to substantiate this This post takes a detailed and critical look at the cost of using concrete instead of steel, the material normally used to construct funicular railways, and concludes that concrete was the more expensive option.
This is quite a long and technical post based on what it would cost to build each 18m section of the funicular consisting of two “I” beams and one in-situ block broken down by the different elements (materials, labour etc). For those not wishing to read the whole post I have highlighted the various sub/running totals with a final costing at the end.
It is difficult to obtain prices for either steel or concrete in 1999 so I have used current prices in the calculations. If anything this strengthens my argument since steel prices and galvanising have increased significantly more than concrete over the last 20+ years.
1. Volumes and cost of materialsrequired to build the funicular
Concrete itself is far cheaper than an equivalent volume steel but to work out the cost depends on the volume of each material required in the construction which in turn is determined by their strength and weight.
(a) 1 x 18m concrete “I” beam.
These are the long beams that sit under and support the funicular track.
Cross section courtesy of the COWI report 2018.
The volume of an “I” beam is the area of the cross section of the beam X the length. I’ll not go into the calculations except to say the area from the section shown above is 156500sq.mm or 0.1565 sq.m. Therefore the volume = 0.1565 x 18 (length of the beam) = 2.817 cubic metres (cu m).
While plain concrete costs about £100 per cu. m. in the case of the funicular “self-compacting” concrete should be used for reasons I will explain later. At a cost of £160 per cu. m the basic costs of the material would be £450. The total weight of an “I” beam at 2.5 tonnes per cu.m. is 7 tonnes.
(b) Steel is much stronger than concrete and therefore the support beam required is much smaller. Based on another funicular I have obtained a price for a steel beam at a size of 610mm x 229mm which comes to £2445 for 18m and a weight of 1.82 tonnes.
Sub-total Concrete £900 v Steel £4890
No contest so far. HIE were completely correct, concrete is cheaper than steel for the same length of beam BUT almost FOUR times the weight.
However,this does not give the total costs.
2. Strengthening the concrete
A concrete beam has to have steel reinforcing bars, commonly called deformed (ribbed) rebar, to give it strength and has to be formed in a purpose-built mould! These bars can be seen in the technical drawing above and picture below.
The purpose of the ribbing is to form a mechanical bond with concrete, therefore preventing longitudinal movement of the bar within the concrete.
Different sizes are used in the concrete “I” beam as follows:-
Diameter. Price per 18m per beam
T8 ( 8mm) £ 25.89
T20 (20mm) £ 56.58 (x4) £226.00
T32 (32mm) £143.67 (x3) £431.00
T40 (40mm) £196.98 (x3) £591.00
(Prices obtained from the website of Steel World UK on 28/04/2023).
You will have noticed that this does not show the price per beam of the T8 rebar as the quantities are not given in the diagram. I have therefore had to make a rough guess as to the quantity, based on the findings of the COWI report into the spacing of the T8, which is used to hold the bigger rebars in position and which I have worked out as follows:.
The length of each T8 link is approx.1.8m and there should be 98 lengths in each beam = a total length of 176.00m x £25.89/18 (to get price per m.) = £253.00.
The total cost of the materials for ONE concrete “I” beam is therefore: Concrete £450 + Rebar £1501 = £1951 and double that for one section.
Running sub-total Concrete £3902 v Steel £4890
So far again HIE’s argument that concrete was cheaper than steel appears to be correct, the difference being £988 per 18m section.
3. Fabrication costs.
This is where it all goes wrong for the argument HIE presented to the Public Accounts Committee.
Steel “H” section beams can be bought “off the shelf”, i.e. ready made and cut to length. Concrete “I” beams have to be made in a mould. Two main elements need to be added to these calculations. They are:-
(a) The cost of the moulds for the concrete “I” beams
To make the concrete “I” beams requires a complex 18m mould, probably made from 18mm Phenolic Film-Faced concrete shuttering plywood, a special type of ply, and 50 x 50 mm timber. This needs to be assembled around the rebar strengthening, the whole structure upside down, and carefully disassembled once the concrete has set. Three different “I” beams were used in the funicular construction and therefore three different designs of mould are required.
While there are two options for making the mould, (i) buy a ready made mould which just needs assembling or (ii) the “I” beam manufacturers make their own, there is little cost difference. I have obtained a “ballpark” quote for a bespoke mould from a company specialising in this type of work, £15,000 for a mould in two 9m lengths + 3 – 4 people and a day to assemble ready for use.
Why upside down you ask? There are polystyrene formers that are part of the mould and will need to be fastened to what will be the bottom of the mould, i.e. top of the “I” beam. These are later removed for the rail fixing bolts, as can be seen in the first pictures in the previous post, to be grouted into place. There are also the sloping ends of the “I” beams to be considered. This is quite labour intensive, not a one-man five-minute job! An 18m timber and plywood mould is also going to take some handling!
A properly made mould is expected to be used for 25 – 30 mouldings so, with the funicular having 186 “I” beams, at least 7 moulds are necessary, two of which have to have built in curves for the type 2 & 3 beams. While a ballpark figure for the straight mould is £15,000 for the more complex type 2 and 3 moulds the cost is about 50% more. The cost per Type 1 “I” beam is therefore £15000 / 30 (the optimum useage) = £500.
Because of the complexity and narrowness of the moulds, which make it almost impossible to use a vibrating-poker, I have used self – compacting concrete in the cost calculations:
Running sub-total Concrete £4902 = Steel £4890
You can see the difference in costs between steel and concrete has now disappeared and there goes HIE’s argument! On top of which there are two further costs which are much more difficult to estimate but are nevertheless significant.
(b) The cost of forming the T8 links
Referring back to the cross-sectional diagram it can be seen that the T8 links are an elongated fig.8 shape. To make that shape and quantity (the total number is 186 x 98 = 18,228) would need at least one rigid former the size of the actual links and a blow torch to help bend the steel, something like this:-
This former would be constructed of 12mm thick plate with 40mm, 32 and 20mm studs welded on. The 98 links for each beam will take some time to shape and probably a workforce of two men!
If it takes 5 minutes to form each link, i.e. 12 per hour, then the cost of those links is two full days wages. Now, depending on what the manufacturer’s hourly labour rate is, that could be as much as £80 x 8( no of hours) x 2( no of workers) = £1280. [I have used £80 as a base figure as it is the current rate charged by a garage. As well as the labour costs there are all the other overheads associated with running a business, i.e N.I., cost of premises etc.] These 98 links then have to be fastened/ welded to each of the 10 x18m lengths of rebar to form the strengthening framework. All this rebar at 18m long, imagine the length of an articulated lorry + 1.5m, has a total weight of 1120.788 kg which is going to take some handling! It also means formers have to be made to keep the rebar in place while the T8 links are welded on.I have not done this kind of work before so I am unable to guess at the cost, but every link will need 14 welds, 1 on each of the T32 & T40 rebars & 2 on each of the T20 rebars, to hold all the rebar together.
Running sub-total Concrete £7462 v Steel £4890
I think I have now proved that the materials cost difference between steel and concrete is at today’s prices quite substantial, with concrete being the more expensive option. Back in 1999 when steel was relatively cheaper it would have been significantly more.
4. Labour costs
(a) The cost of the insitu joints
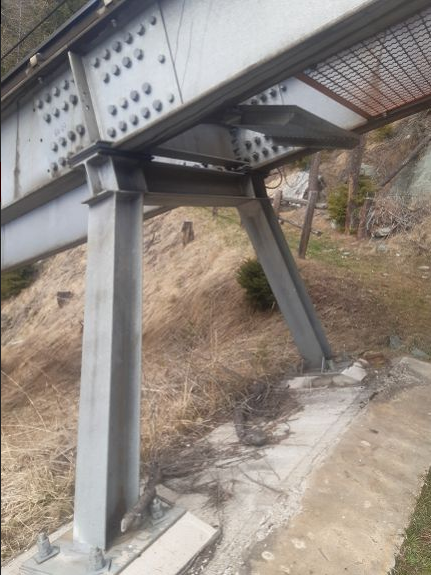
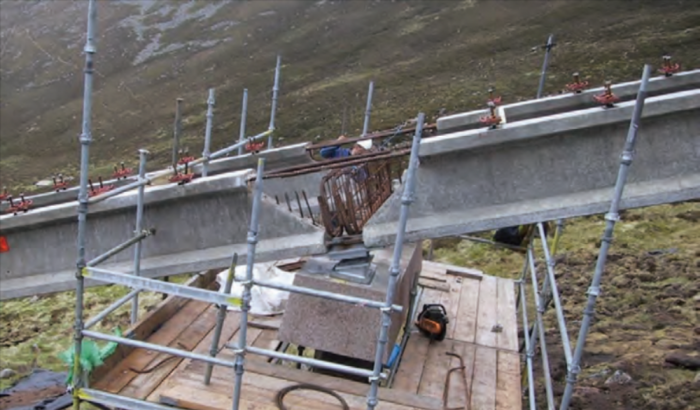
Compare the pictures above of the joints in the steel beams of the Frachey funicular to the concrete insitu joints on the HIE funicular. Steel uses pre-drilled plates and some eighty nuts and bolts, assembly time two people for 1 day tops.
Approximate labour cost, using the same estimated labour cost of £80 per hr, £80 x 8hrs x 2 (steel erectors) = £1280.
The concrete insitu joints need, again using the same estimated labour cost of £80 per hr:
Day one. A qualified welder for one day to weld all the steel work into place.
Approximate cost £ 640.
Day two. A steel worker and welder to fabricate and fix the reinforcing cage.
Approximate cost £640
Day three. 3 – 4 shuttering joiners for one day to fabricate the mould.
Approximate cost £1920 (minimum)..
Day four. 1 x scaffolder to assemble the supporting scaffolding for the mould and 1 x concreter possibly getting the concrete poured that same day.
Approximate cost £1280
Day five and possibly six allowing the concrete time to set, and finally,
Day seven. Removing all shuttering and scaffolding.
Approximate labour cost £640 minimum.
Approximate total £5120.
SEVEN DAYS and eight tradesmen to complete a job that if made in steel could have been done in ONE by two tradesmen. OVERRUN COSTS!!!
Running sub – total Concrete £12,582 v Steel £6170
I have made a cardboard model to show exactly how complicated the outer ends of the mould would look:-
3
On the inside of the mould the shape is the same but the upstand of “T”, part no 1, and sides 4 & 5 would be replaced by shuttering connecting the two “I” beams together.
(b) Assembly costs
I have no qualifications to determine accurately the labour costs of assembling concrete v steel but look again at the first two pictures at the beginning of the post and it is plain to see which funicular is easier and quicker to build! Steel wins out every time.
However, then add in the challenges of constructing a funicular in an environment like Cairn Gorm. Because of the amount of labour required on site, using concrete rather then steel made the whole project far more vulnerable to delays by the weather, as recorded by Morrison’s in the health and safety file, increasing costs.
5. Other construction costs
These calculations have not even begun to factor in other costs, from the larger foundations required to support the heavier concrete “I” beams to the comparative cost of transporting steel v concrete “I” beams to the site.
6. Maintenance costs of concrete v steel
While it was probably assumed that concrete would require small maintenance costs that has now been proved to be wrong by about £25,000,000 or the amount it has cost to repair the funicular! That’s an average of roughly £260,000 per 18m section (crosshead, “I” beams, insitu joint and piers), or £15,000 per annum. Or look at it this way. £25,000,000 for 17 years of actual use is a cost of almost £1,500,000 per annum. Is that what repair/ maintenance costs will average in the future?
Plain, untreated steel on the other hand would require painting under a regular expensive maintenance regime. The answer therefore would be to use hot dipped galvanised steel which would be expected to last 50+ years WITHOUT ANY MAINTENANCE. Today’s cost to have an “I” beam galvanised is about £500 per tonne or a total of £910!
Total cost per section Concrete £12582 v Steel £7990
Conclusion
This post has shown that HIE’s claim to the Public Audit Committee that concrete was cheaper than steel was totally unfounded. Indeed, while this claim has never been properly examined up until now, when you consider the factors I have described here it should be perfectly obvious why the current cost of the funicular construction and maintenance, in excess of £50m, was so much more than the original budget.
Given all of this my next post (Friday) will consider the real reasons HIE chose concrete over steel, which clearly had nothing to do with it being cheaper, and the implications of this disastrous decision for the future.
Two excellent articles so far Graham. From my professional construction knowledge, life cycle costings will always show steel to be cheaper than reinforced concrete for this type of structure. I have seen and travelled on several funicular railways in Europe and all of of them have been constructed in steel. I look forward to your concluding article!
Interesting detailed ‘analysis’ of materials costings, workmanship and installation of concrete versus steel.
May i ask if you have an Engineering background and secondly, do you know if it is possible to acquire a copy of the COWI structural report ?
Regards.
Very interesting analysis, Graham. You and your colleagues at ParksWatchScotland have clearly put enormous effort into trying to unravel the shocking story of ’21st century Cairngorm and its funicular’. It’s commendable – of great public benefit.
The killer factors in the end will surely be:
– the combination of the environmental impact of this huge structure on the fragile Gorm landscape and what happens to the mountain when it’s removed
– the cost of destroying/removing/recycling it.
Whether it is actually possible or viable to recycle the funicular structure is debatable … but it’s obvious that removal of an all-steel structure would be far far easier, cheaper and less impactful. And all that steel would be readily melted down to produce other stuff.
It is said that the original plan of the scheme was for HIE/Cairngorm Mountain to hold a financial bond sufficient to remove the funicular in the end. That’s another thing to investigate. What do the enterprises’ minutes reveal, as to that decision-making?