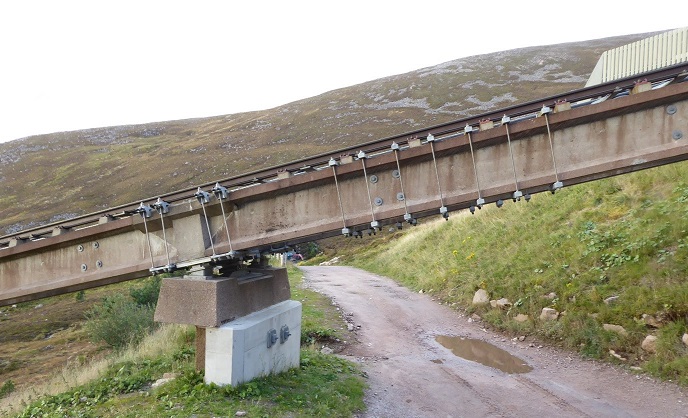
On Friday 04/10/2024, prompted by HIE’s announcements about the timecale for the “snagging works” being carried out and paid for by Balfour Beatty (see here), I took a walk up to the passing loop of the funicular accompanied by two friends.
Following what I had written last December (see here) I expected to see changes/ repairs that would be instantly recognisable as such, e.g. more of the type 1 brackets and/ or larger support plates under the Type 3 brackets as labelled in the following picture:-
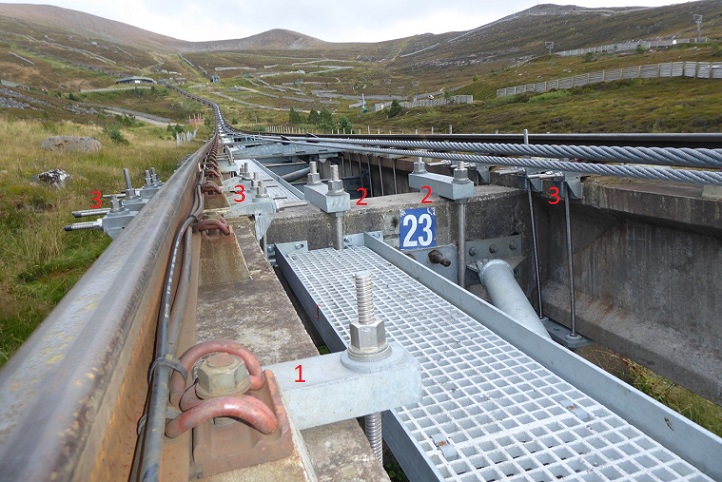
Instead we found this:-
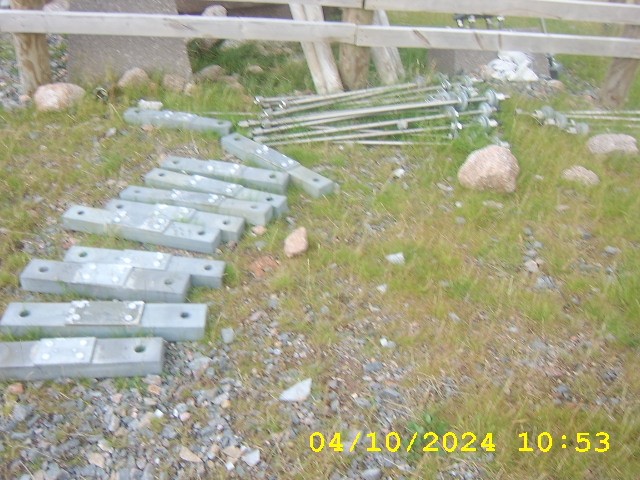
and this:-
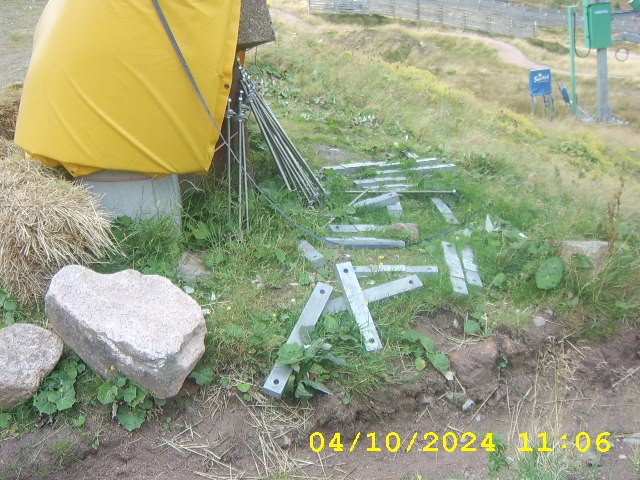
The Current Works
The whole point of the snagging works according to HIE was for the Type 2 & 3 strengthening rods and brackets to be re-torqued and re-tensioned, as per the following press release on 06/09/2023:-
Notice there is no mention of any problem with the Type 1 brackets used to strengthen the “I” beams, until another press release (see here) on 15/04/2024;-
Para. 3 refers to “tensioning works to beams and diaphragms”. “Beams” obviously refers to the concrete “I” beams, presumably “diaphragms” therefore are the insitu concrete joints. It looks as though HIE may have deliberately changed their names for different parts of the funicular structure in order to confuse the ordinary person.
You cannot test the tension, however, until AFTER works are completed! If the tension is not as required THEN you carry out adjustments until the correct tensioning is obtained. The claim in March that “testing is under way on tensioning works” therefore appears another load of nonsense
If that tensioning work was ever completed it now has to be done all over again as almost all of the Type 1 brackets have been removed as shown in the photos above of Type 1 brackets lying on the ground.
There were also some parts of brackets lying on the funicular beam and on the scaffolding at the passing loop:
Para 6. “We are working hard……multiple teams…….to resume service before the next winter snowsports season”.
We saw TWO teams working but maybe the “multiple teams” is because people are working at all hours and seven days a week?
The next screenshot is from CMSL’s accounts which have been recently published and is part of the chairman’s statement of 31/03/2024 :-
As all the removed brackets are refitted or replaced grout needs to be inserted between them and the the concrete. An extract from the third picture shows where the grout has been:
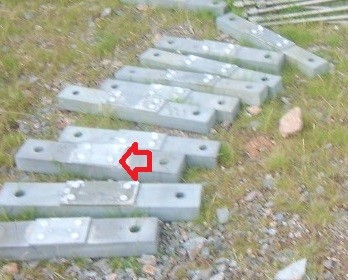
If regrouting the brackets is not possible in winter as the chair of CM(S)L Peter Mearns claims, not only was his statement in March that the funicular would “Resume service before the next winter snowsport season” wrong, it means all the latest claims from HIE/CM(S)L that it will re-open this winter must also be untrue. So, why are they trying to convince their loyal customers to buy season passes when their chairman has effectively explained that the current work will not be finished before spring 2024?
By my reckoning over 800 of the 917 Type 1 brackets had been removed from the “I” beams by the time of my visit, all of which have to be replaced, tensioned, tested THEN adjustments made and re-tested!
Material issues with the brackets.
The nuts and studding used in the brackets are made of stainless steel which has a very low rate of heat conductivity and is a notoriously difficult material to work with:
(a) when cutting or drilling stainless steel it will eat angle grinder discs, hacksaw blades and drill bits, and/or;
(b) when fastening or removing nuts using powered equipment such as an impact driver – as in the case of the brackets on the funicular – the threads tend to overheat, deform, jam or spall which can result in either the studding snapping or having to be cut with an angle grinder.
The fact that new metal studding (see photo above) is being used suggests that this is what has happened with the brackets round the beams. The way to prevent this is to use either water or a thin oil as a lubricant, although even that can alter the tightening torques, but this would require the work to progress more slowly. Water is actually preferable as you can see the steam if the work gets too hot!
The other major problem with these works is the varying temperatures on the day a bracket is tensioned. On a hot day the steel will have expanded slightly which when cooling increases the tension and therefore pressure on the concrete that it is supposed to be strengthening. Conversely tightening/ tensioning on a cold day means the tension will be changed/ reduced again on the next hot day. This cycle could happen several times a day AND have different effects depending on which side of the beam is in shade.
Conclusion.
The fitting of the stainless steel and galvanised brackets has one function, to try to strengthen the concrete “I” beams and this could have worked in a less hostile environment. The temperature range on Cairn Gorm however can vary by as much as 58°c and that will continue to cause problems no matter how much steel is added.
Concrete was not a suitable material with which to build the funicular (see here) and there appear to be other problems with the “I” beams which I will discuss in the next post.
I’d like here to take the opportunity to thank Mr Ian Joy an experienced project manager who, at my request, gave an interview to the Press & Journal (see here) about his experience of being interviewed as manager for Cairn Gorm.
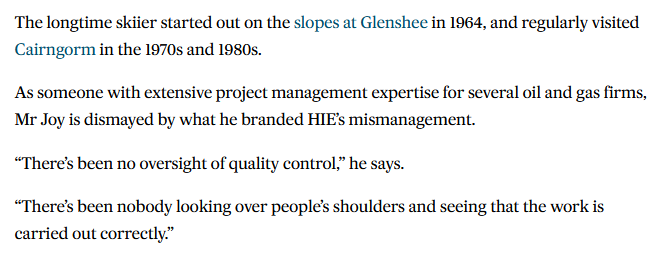
I have also been in contact with other civil engineers and people who worked on the initial build and it appears that some of them may now prepared to follow My Joy’s example.
As an engineer I agree with much of what you’ve said. The big problem is that we’re hearing nothing from Cairngorm on the issue. They should be publicly accountable and have taken steps to explain the engineering choices, there may be factors which make their choices the correct ones. We’re not building anything secret here, there’s no reason why the engineering decisions can’t be explained in public. Not engaging with the public will naturally lead to speculation.